Silver Use: Changes & Outlook
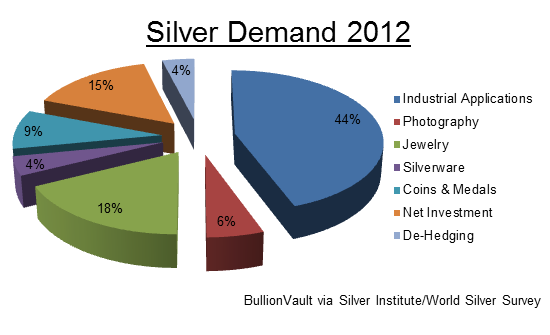
We use cookies (including third-party cookies) to remember your site preferences, to help us understand how visitors use our sites and to make any adverts we show on 3rd party sites more relevant. To learn more, please see our privacy policy and our cookie policy.
To agree to our use of cookies, click 'Accept' or choose 'Options' to set your preferences by cookie type.
Vice president of business development for BullionVault from 2012 to 2014, Miguel Perez-Santalla is a fierce advocate for retail investors, and a regular speaker at industry and media events. With over 30 years' experience in the precious metals business, Miguel has worked at the United States' top coin dealerships, as well as international refining group Heraeus.
See the full archive of Miguel Perez-Santalla articles.
Please Note: All articles published here are to inform your thinking, not lead it. Only you can decide the best place for your money, and any decision you make will put your money at risk. Information or data included here may have already been overtaken by events – and must be verified elsewhere – should you choose to act on it. Please review our Terms & Conditions for accessing Gold News.
We use cookies to remember your site preferences, record your referrer, improve the performance of our site and to make any adverts we show on 3rd party sites more relevant. For more information, see our cookie policy.
Please select an option below and 'Save' your preferences.
You can update your cookie preferences at any time from the 'Cookies' link in the footer.
You have not been active for some time.
For your security you will be logged out in minutes unless you take action.